Herrid´s Vitrification Kit for camel embryos
The efficiency of cryopreservation of camel embryos has been significantly improved by applying vitrification techniques. In comparison to slow controlled-rate freezing, vitrification is a simple and successful technique. It is based on a combination of media containing highly concentrated cryoprotective agents allowing rapid cooling and thawing rates which avoid or reduce ice crystal formation and thus improve the survival of cells.
First and only commercial media kit proven to be efficient for camel embryos
Herrid’s Vitrification Kit is a media kit for vitrification and thawing up to 30 camel embryos. It has been proven to be effective in cryopreserving camel embryos (90% survival rate) and resulting in about 50% pregnancy rate. This vitrification protocol is designed for day 6 – day 8 camel embryos. The diameter of the embryo is a key element for optimum results of the vitrification process (ideal diameter between 350 and 650 μm).Your benefits
- Tested and proven: Herrid's Vitrification Kit is the first and only commercial media kit which has been proven to be efficient for camel embryos
- Ready-to-use media
- Gas-tight packaging for longer shelf life
- Convenient package sizes
- Manufactured under GMP conditions in dedicated clean room
- Quality control of each batch performed under veterinarian supervision
- Batch certificate available
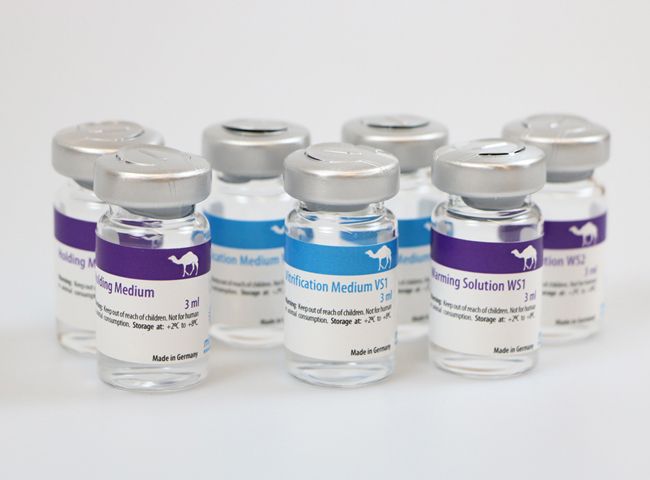