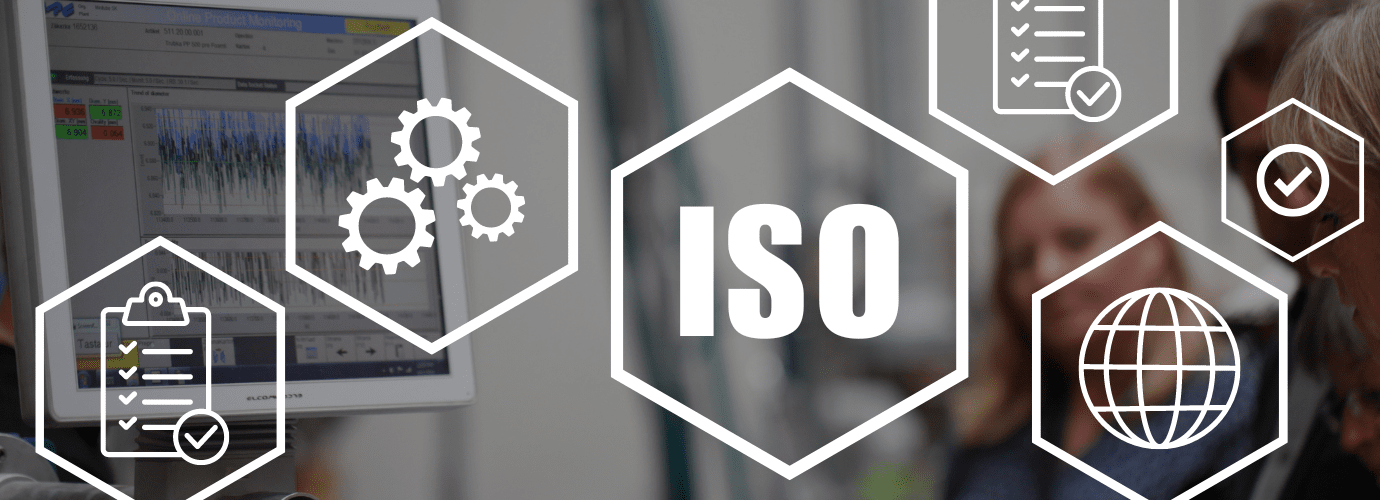
Quality Management
Minitube is totally committed to quality – this is at the core of everything that we do.
For our worldwide client base, we recognize that reliability, functionality, and efficiency are key factors for running a stress-free and profitable production system. For over 50 years Minitube has delivered robust, high-performance, quality equipment and consumables to the assisted reproduction market.
As an industry leader, we accept the responsibility of providing products that do not compromise quality or safety. For this reason, all proprietary consumables and semen or embryo preservation media are manufactured in our own dedicated state-of-the-art facilities, supported by extensive in-house and external third-party QA testing you can trust. There are approximately 3,000 double checks performed during incoming inspections of samples per year. To put it in concrete terms: Narrow product tolerances apply here, such as a measuring length with an accuracy of up to 0.0001 mm! Minitube quality is not subjective but based on hard facts and decades of a successful track record.
Our total quality approach is underpinned by a long-term partnership strategy with our suppliers and customers. These long-standing relationships help build the trust and understanding required to ensure ongoing quality.
The same is true for our service team who are always striving to provide the best service within the industry. As a customer, the expert knowledge and know-how of Minitube staff is always available to you.
The ISO 9001:2015 certificate proves that all internal processes are being surveyed by the worldwide technical inspection authorities at regular intervals and comply with international quality management standards. The process oriented standard ISO 9001:2015 lends great importance to a continuous improvement process within the company and to an increase in customer satisfaction. Since 2011, our extender production in Germany is GMP-certified.
The certification demonstrates Minitube's clear commitment to quality, continuous improvement and to the central importance of customer satisfaction at all company levels.
The German headquarters was certified as early as 2004 and the quality management system in practice has been checked and improved year after year since then. In 2023, after Minitüb GmbH, Minitüb Slovakia, and Minitub do Brasil, Minitube USA is the fourth subsidiary to have earned the ISO-certified status, reflecting the high quality standards across all members of the group.
Minitube's aim is the continuous improvement of all processes within our company, particularly concerning product development, production, and product quality. This includes regular consultations with our customers, an effective feedback and complaint handling system, an employee suggestion system as well as internal and external audits. All these efforts mean that we can respond even faster and more effectively to the requirements and wishes of our customers.
For our clients worldwide, production reliability is a key factor for working profitably. Only sound and high-grade equipment will lead to constant, uninterrupted operation – working day by working day. Minitube consistently delivers reliable and quality products, as extremely low complaint rates prove.
For our worldwide client base, we recognize that reliability, functionality, and efficiency are key factors for running a stress-free and profitable production system. For over 50 years Minitube has delivered robust, high-performance, quality equipment and consumables to the assisted reproduction market.
As an industry leader, we accept the responsibility of providing products that do not compromise quality or safety. For this reason, all proprietary consumables and semen or embryo preservation media are manufactured in our own dedicated state-of-the-art facilities, supported by extensive in-house and external third-party QA testing you can trust. There are approximately 3,000 double checks performed during incoming inspections of samples per year. To put it in concrete terms: Narrow product tolerances apply here, such as a measuring length with an accuracy of up to 0.0001 mm! Minitube quality is not subjective but based on hard facts and decades of a successful track record.
Our total quality approach is underpinned by a long-term partnership strategy with our suppliers and customers. These long-standing relationships help build the trust and understanding required to ensure ongoing quality.
The same is true for our service team who are always striving to provide the best service within the industry. As a customer, the expert knowledge and know-how of Minitube staff is always available to you.
ISO 9001:2015 certificate
The ISO 9001:2015 certificate proves that all internal processes are being surveyed by the worldwide technical inspection authorities at regular intervals and comply with international quality management standards. The process oriented standard ISO 9001:2015 lends great importance to a continuous improvement process within the company and to an increase in customer satisfaction. Since 2011, our extender production in Germany is GMP-certified.The certification demonstrates Minitube's clear commitment to quality, continuous improvement and to the central importance of customer satisfaction at all company levels.
The German headquarters was certified as early as 2004 and the quality management system in practice has been checked and improved year after year since then. In 2023, after Minitüb GmbH, Minitüb Slovakia, and Minitub do Brasil, Minitube USA is the fourth subsidiary to have earned the ISO-certified status, reflecting the high quality standards across all members of the group.
What are the advantages for Minitube customers?
Minitube's aim is the continuous improvement of all processes within our company, particularly concerning product development, production, and product quality. This includes regular consultations with our customers, an effective feedback and complaint handling system, an employee suggestion system as well as internal and external audits. All these efforts mean that we can respond even faster and more effectively to the requirements and wishes of our customers.For our clients worldwide, production reliability is a key factor for working profitably. Only sound and high-grade equipment will lead to constant, uninterrupted operation – working day by working day. Minitube consistently delivers reliable and quality products, as extremely low complaint rates prove.