Minitube quality management: our commitment, your benefit
“Quality is the best way to reduce costs.”
It is stated in our company mission, in our certificates and not least in our minds: With all our activities, Minitube is committed to quality. Our aim is the continuous improvement of all processes within the company, particularly concerning product development, production and product quality. This includes regular consultations with customers, an effective feedback and complaint handling system, an employee suggestion system in addition to internal and external audits. Minitube is committed to the constant optimization of all processes, allowing faster and more effective responses to requirements of the customers.
As an industry leader, we recognize the importance of providing products that do not compromise quality or safety even if this should result in higher production costs. For this reason, all proprietary products are manufactured in our own state-of-the-art facilities and double checked by on-line process monitoring at the production site as well as at in our quality management department in Germany. There are approximately 3,000 double checks performed during incoming inspections of samples per year. Narrow product tolerances apply here, such as a measuring length with an accuracy of up to 0.0001 mm. Minitube quality is not subjective but rather strict hard facts.
But what does that mean for our customers? For our clients worldwide, production reliability is a key factor for working profitably. Only sound and high-grade equipment will lead to constant, uninterrupted operation – working day by working day. Minitube consistently delivers on reliable and quality products, as extremely low complaint rates prove.
It is stated in our company mission, in our certificates and not least in our minds: With all our activities, Minitube is committed to quality. Our aim is the continuous improvement of all processes within the company, particularly concerning product development, production and product quality. This includes regular consultations with customers, an effective feedback and complaint handling system, an employee suggestion system in addition to internal and external audits. Minitube is committed to the constant optimization of all processes, allowing faster and more effective responses to requirements of the customers.
As an industry leader, we recognize the importance of providing products that do not compromise quality or safety even if this should result in higher production costs. For this reason, all proprietary products are manufactured in our own state-of-the-art facilities and double checked by on-line process monitoring at the production site as well as at in our quality management department in Germany. There are approximately 3,000 double checks performed during incoming inspections of samples per year. Narrow product tolerances apply here, such as a measuring length with an accuracy of up to 0.0001 mm. Minitube quality is not subjective but rather strict hard facts.
But what does that mean for our customers? For our clients worldwide, production reliability is a key factor for working profitably. Only sound and high-grade equipment will lead to constant, uninterrupted operation – working day by working day. Minitube consistently delivers on reliable and quality products, as extremely low complaint rates prove.
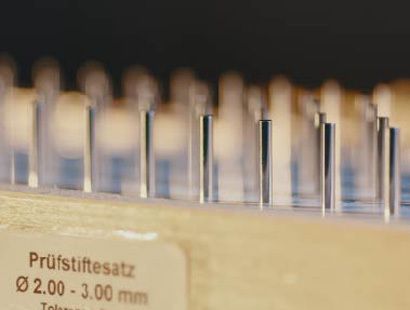